Isolationslösung für Keramikfaser im Feuerverzinkungsofen
Die Feuerverzinkungstechnologie ist ein energieintensiver Produktionsprozess. Mit der Förderung der Energieeinsparung in China ist die energiesparende Isolationsarbeit in der Feuerverzinkungsindustrie von entscheidender Bedeutung geworden. In kontinuierlichen Feuerverzinkungsproduktionslinien entfällt etwa sechzig bis siebzig Prozent des Gesamtenergieverbrauchs auf den Glühofen für die Feuerverzinkung. Daher ist die Isolierung des Glühofens für die Feuerverzinkung ein ausgezeichnetes Anwendungsgebiet für Produkte aus Keramikfasern.
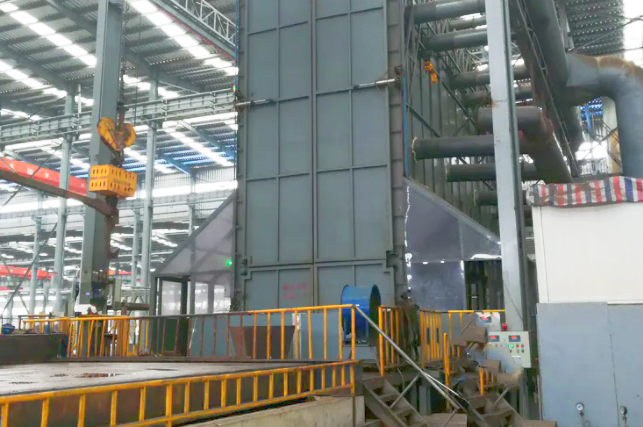
1. Isolationslösungen für verschiedene Abschnitte des Glühofens für das Feuerverzinken
Der kontinuierliche Feuerverzinkglühofen dient als Auftakt zum Eintauchen in den Verzinkungstopf. Er ist hauptsächlich in den Heizabschnitt, den gleichmäßigen Heizabschnitt und den Schnellabkühlabschnitt unterteilt.
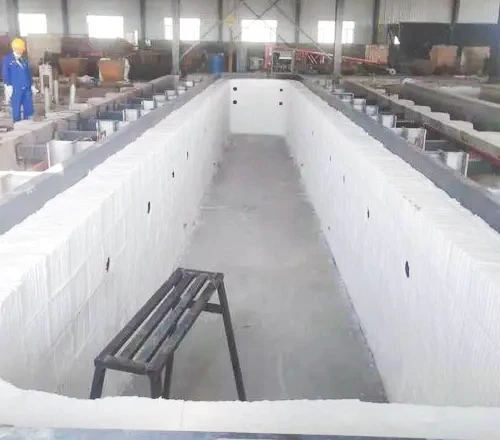
a) Heizabschnitt
Im Heizabschnitt liegt der Schwerpunkt auf der Oxidations-Reduktionsbehandlung der Oberflächen der Eisenplatten. Dies geschieht größtenteils mit gasbeheizten Strahlrohren zur Beheizung. Die Temperatur wird unter 1000 °C gehalten. Für diesen Temperaturbereich werden hauptsächlich Standard-Keramikfaser-Module für die Seitenwände und das Dach verwendet. Der Ofenboden ist mit feuerfesten Ziegeln gepflastert und mit Calciumsilikatplatten ergänzt.
b) Abschnitt der gleichmäßigen Erwärmung
In diesem Abschnitt erfolgt die Erwärmung hauptsächlich durch Widerstandsdraht, ohne offene Flamme. Der Ofenboden ist ebenfalls mit feuerfesten Ziegeln gepflastert, die Rillen für die Verlegung der Widerstandsdraht bilden. Die Seitenwände und das Dach sind hauptsächlich mit keramischen Fasermodulen ausgestattet.
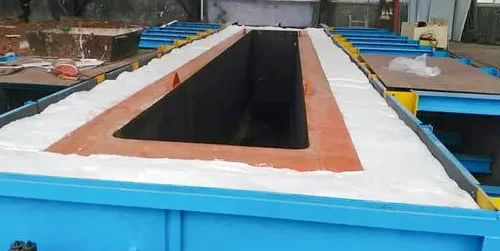
c) Schnellkühlabschnitt
Im Schnellkühlabschnitt, der der nachfolgende Schritt vor dem Eintauchen der Eisenplatte in den Zinktopf ist, muss eine schnelle Abkühlung auf unter 560°C erfolgen. In diesem Temperaturbereich werden Hochgeschwindigkeitsventilatoren verwendet, um die Eisenplatte zu kühlen, daher erfordert die Isolationsarbeit in diesem Temperaturbereich besondere Aufmerksamkeit. Die Ofenseitenwände und das Dach sind mit keramischen Faserdecken isoliert, der Ofenboden ist mit Calciumsilikatplatten bedeckt. Zusätzlich werden rostfreie Stahlplatten verwendet, um den Innenofen abzudecken. Aufgrund des Hochgeschwindigkeitsluftstroms in diesem Temperaturbereich hilft das Platzieren einer Schicht rostfreier Stahlplatten, das Verstreuen der Fasern zu verhindern und ein Anhaften an der Eisenplatte zu vermeiden. Es bewahrt auch effektiv die Integrität der Isolationsmaterialien. Für die Behandlung des Ofendeckels im Schnellkühlabschnitt werden Isolations-Keramikfaserwatte und rostfreie Stahlplatten für eine umfassende Abdichtung verwendet.
2. Isolationslösung für den Abschnitt des Feuerverzinkungsbads
Der Prozess des Verzinkens von Eisenplatten in einem Zinkbad beinhaltet eine Wärmebehandlung. Dieser Prozess erfordert auch die Verwendung von Keramikfasermodulen zur Isolierung im Ofen, der zum Erhitzen des Zinkbads verwendet wird. Das Hochtemperatursegment in diesem Bereich befindet sich hauptsächlich in der Nähe der Brenner des Ofens, die sich an den beiden Enden des Zinkbads befinden und Temperaturen von etwa 1100°C oder niedriger haben. Die Isolierschicht in diesem Bereich muss dicker sein.
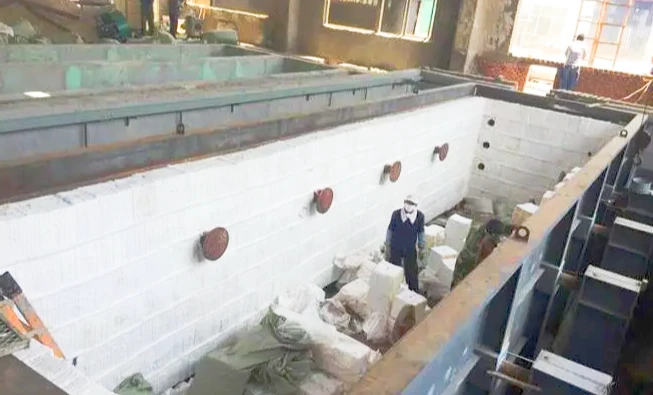
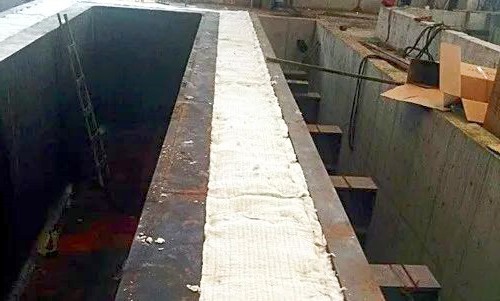
Im Isolationsabschnitt des Zinkbads verwenden die meisten Ofenunternehmen immer noch vorwiegend Keramikfaser-Module, während sich eine kleine Anzahl von Ofenunternehmen für feuerfeste Ziegel und Gießmassen entscheidet. Die Isolierleistung und Integrität von feuerfesten Ziegeln und Gießmassen sind jedoch beide schlechter als die von Keramikfaserprodukten. In Bezug auf Installation und Bau sind Keramikfaser-Module im Vergleich zu feuerfesten Ziegeln und Gießmassen ebenfalls viel bequemer.