Keramikfaserisolierungsschema für Karbonisierofen
Überblick über den Karbonisierofen
Einführung in den Karbonisierofen
Der Karbonisierofen ist eine Art thermischer Ausrüstung, die für die indirekte Beheizung verschiedener Kohlenstoffprodukte unter Bedingungen hoher Drücke verwendet wird. Dieser Prozess erfolgt bei festgelegten Karbonisierungstemperaturen in einer sauerstoffarmen Umgebung, um die Leitfähigkeit und thermischen Eigenschaften der Produkte zu verbessern und somit deren Festigkeit zu steigern.
Isolationsstruktur des Karbonisierofens
Die Isolierung des Karbonisierofens ist in den Ofenboden, die Seitenwände, die Verbrennungswände, die Querwände, den Ofendeckel und den Rauchkanal unterteilt.
Arten von Karbonisieröfen
Es gibt zwei Arten von Karbonisieröfen: offene kreisförmige und geschlossene kreisförmige Typen. Diese werden hauptsächlich für das Backen von Kohlenstoffanoden für Aluminium und für das Backen von Stahlelektroden verwendet. Derzeit werden offene kreisförmige Karbonisieröfen für das Backen von Aluminium-Kohlenstoffanoden verwendet.
Die Produktionspraxis zeigt, dass die Wärmeausnutzung und der Wärmeverlust des Karbonisierofens jeweils etwa fünfzig Prozent ausmachen. Daher ist die Reduzierung des Brennstoffverbrauchs im Backprozess von Aluminium-Kohlenstoffanoden seit langem ein bedeutendes Problem in der Kohlenstoffindustrie.
Produktionsherausforderungen des Karbonisierofens
Schwere Unterdrucklecks, instabiler Betrieb, erheblicher Wärmeverlust und verringerte Produktqualifikationsraten erhöhen die Kosten für Unternehmen. Unterdrucklecks treten hauptsächlich aufgrund schlechter Qualität, Verformbarkeit und leichter Rissbildung von Ofenwandmaterialien auf, was Schwierigkeiten bei der Erzeugung von Unterdruck verursacht.
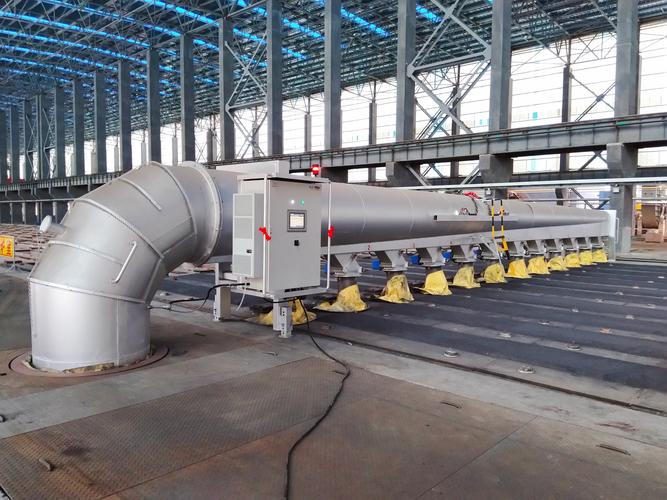
Keramikfaserisolierungsschema
(1) Isolierung des Imprägniersystems
Isolationsstruktur des Imprägnierheizofens
Der Imprägnierheizofen, auch als Vorwärmofen bekannt, arbeitet bei Temperaturen von maximal 650°C, wobei die Brennkammer bei 800°C mit Gas beheizt wird.
Es verwendet eine Verbundstruktur aus Keramikfaserdecken vom Typ 1050 und Keramikfasermodulen vom Typ 1050. Die Ofenwände, Wände und Türen haben eine Isolationsdicke von 280 mm, bestehend aus einer 30 mm dicken Keramikfaser-Unterdecke vom Typ 1050 und einem 250 mm dicken Keramikfasermodul vom Typ 1050. Die Ofenoberseite hat eine Isolationsdicke von 350 mm, mit einer Struktur aus einer 50 mm dicken Keramikfaser-Unterdecke vom Typ 1050 und einem 300 mm dicken Keramikfasermodul vom Typ 1050.
Isolationsstruktur der Verbrennungskammer oben im Heizofen
Die Isolationsdicke beträgt 350 mm, bestehend aus einer 50 mm dicken Keramikfaser-Unterdecke vom Typ 1050 und einem 300 mm dicken Keramikfasermodul vom Typ 1050.
Externe Isolationsstruktur des Imprägnierbehälters
Die Betriebstemperatur des Imprägnierbehälters beträgt 300°C. Um Verbrennungen der Arbeiter, Wärmeverlust und Korrosion zu verhindern, ist eine externe Isolierung erforderlich.
Die Isolationsschicht besteht aus einer 100 mm dicken Keramikfaserdecke vom Typ 1050 und einer 0,5 mm dicken farbigen Stahlplatte. Aufgrund der unterschiedlichen Tankgrößen und -zahlen wird empfohlen, ein professionelles Bauteam zu beauftragen, um Stahlrahmen nach Bedarf zu installieren.
(2) Backsystem: Entwurf der Isolationsstruktur für kreisförmige Backöfen
Arbeitstemperatur der Ofenauskleidung
Die Langzeit-Arbeitstemperatur beträgt 1250°C bei Gasheizung.
Ofenauskleidungsmaterial
Es verwendet eine Verbundstruktur aus zirkoniumhaltigen Keramikfasermodulen und zirkoniumhaltigen Keramikfaserdecken. Die Isolationsdicke beträgt 350 mm, bestehend aus einer 50 mm dicken zirkoniumhaltigen Keramikfaser-Unterlage und einem 300 mm dicken zirkoniumhaltigen Keramikfasermodul.
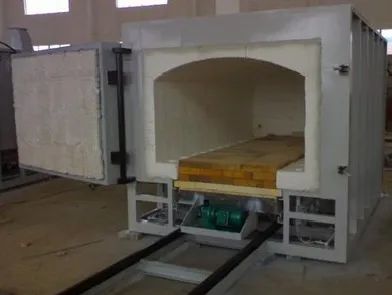